How Concrete is Made?
From Raw Materials to Solid Foundations
Concrete is the backbone of modern construction, providing strength and durability to countless structures worldwide. From skyscrapers to highways, concrete plays a pivotal role in shaping our built environment. But have you ever wondered how this seemingly mundane material is created? In this article, we’ll take you through the intricate process of making concrete, from its raw ingredients to its final form.
Concrete is the foundation of modern construction projects, from residential homes to massive infrastructure developments. Its remarkable strength, versatility, and affordability have made it an essential material in the construction industry. Let’s delve deeper into the process of how concrete is made.
Understanding Concrete Composition
What is Concrete?
At its core, concrete is a composite material composed of cement, aggregates, water, and often additional additives known as admixtures. The precise ratio of these components determines the properties of the concrete and its suitability for various applications.
Components of Concrete Mixture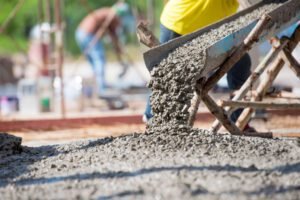
Concrete’s strength and durability come from its careful balance of ingredients. The primary components include:
- Cement: The binding agent that holds the mixture together.
- Aggregates: Inert granular materials, such as sand and gravel, that provide bulk and stability.
- Water: A crucial element for the hydration process that transforms cement into a solid matrix.
The Role of Cement
Cement Production
Cement is manufactured by extracting raw materials like limestone and clay from quarries and subjecting them to high temperatures in a kiln. The resulting clinker is finely ground to produce cement powder, which serves as the glue that binds the concrete mix together. For buying best quality cement visit here.
Types of Cement
Various types of cement are available to suit different project requirements. Ordinary Portland Cement (OPC) is commonly used, but specialty options like Portland Pozzolana Cement (PPC) and Sulphate-Resistant Cement (SRC) offer specific advantages.
Aggregates: The Backbone of Concrete
Types of Aggregates
Aggregates are divided into fine and coarse categories. Fine aggregates, like sand, provide workability and fill the voids between larger particles. Coarse aggregates, such as gravel, contribute to the concrete’s strength and stability.
Aggregate Selection
Choosing the right type and size of aggregates is crucial for achieving the desired concrete properties. Proper selection ensures optimal compaction and overall durability.
Creating the Concrete Blend
Mixing Techniques
The process of blending cement, aggregates, and water is critical to forming a homogeneous mixture. Different methods, such as batch mixing and continuous mixing, are employed based on project needs.
Water-Cement Ratio Importance
Controlling the water-cement ratio is crucial for concrete strength and durability. Excess water weakens the mix, while too little hinders workability. Engineers balance this ratio to ensure optimal performance. Too much water creates porous, weak concrete prone to cracks. Too little water makes the mix stiff and hard to shape. Achieving the right balance considers factors like desired strength, environmental conditions, and aggregate types. Chemical admixtures can fine-tune the ratio. In essence, the water-cement ratio is a fine-tuned formula for durable, workable concrete structures.
Admixtures
Types of Admixtures
Admixtures are additives that modify the properties of concrete. They can improve workability, accelerate or delay setting times, and enhance durability. Common types include plasticizers, accelerators, and air-entraining agents.
Effects on Concrete Properties
Each admixture type imparts specific benefits. For instance, plasticizers increase workability, while air-entraining agents improve freeze-thaw resistance.
Concrete Placement and Formwork
Pouring Techniques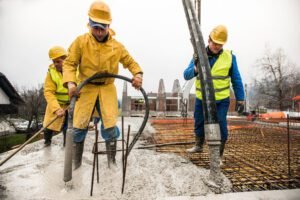
Pouring concrete requires careful planning for even distribution in formwork. Techniques like pumping, pouring, and placing ensure uniform coverage. Pumping moves concrete to the site, pouring fills the formwork, and placing arranges it accurately. These methods guarantee structural integrity and a lasting finish.
Importance of Formwork
Formwork holds the concrete in place as it cures, determining the final shape and surface finish of the structure. Properly designed formwork is essential for achieving desired aesthetics and structural integrity.
Ensuring Strength and Durability
Curing Methods
Curing involves maintaining adequate moisture and temperature conditions for the concrete to develop its full strength. Methods range from moist curing to using curing compounds.
Time and Temperature Factors
Curing duration and temperature significantly impact the concrete’s ultimate strength and durability. Adequate curing is crucial for long-term performance.
Finishing Touches
Texturing and Smoothing
After curing, concrete surfaces can be textured and smoothed to enhance aesthetics and functionality. Techniques like brushing, stamping, or polishing create distinct finishes.
Coloring and Staining
Concrete can be colored using pigments or stained to mimic natural materials. These techniques offer design flexibility and aesthetic appeal.
Quality Control in Concrete Production
Testing Procedures
Stringent testing ensures that the concrete meets specified standards. Compression tests, slump tests, and moisture content checks verify consistency and quality.
Ensuring Structural Integrity
Thorough quality control guarantees that the final concrete structure will be safe, durable, and capable of withstanding its intended load.
Sustainability in Concrete Manufacturing
Eco-Friendly Practices
The concrete industry is making strides toward sustainability by using recycled materials, reducing energy consumption, and minimizing waste production.
Recycled Materials Usage
Recycled aggregates and supplementary cementitious materials like fly ash and slag can replace traditional raw materials, lessening the environmental impact.
Innovations in Concrete Production
Self-Healing Concrete
Researchers are developing concrete that can repair its own cracks, prolonging the lifespan of structures and reducing maintenance costs.
3D-Printed Concrete
Additive manufacturing techniques are revolutionizing construction by enabling the creation of intricate and customized concrete components.
Challenges and Future Outlook
Addressing Carbon Footprint
Concrete production contributes to carbon emissions. Ongoing research aims to develop low-carbon cement and carbon capture technologies.
Technological Advancements
The industry is embracing digital tools for better project management, quality control, and design optimization.
Conclusion
Concrete, a remarkable material derived from simple components, has transformed the way we build. From towering skyscrapers to humble sidewalks, its versatility and strength have stood the test of time. Understanding the meticulous process behind creating concrete enhances our appreciation for the structures that shape our world. For more informative blogs and articles visit here or visit our website https://cronusconcrete.com/
Frequently Asked Questions
Q1.Is concrete environmentally friendly?
Ans.Concrete can be made more sustainable by using recycled materials and implementing energy-efficient production methods.
Q2.What is the role of water in concrete?
Ans. Water initiates the chemical reaction that allows cement to harden, forming a solid structure.
Q3. Can concrete be repaired if it cracks?
Ans. Self-healing concrete is an innovative solution that can autonomously repair small cracks, extending the lifespan of structures.
Q4. How is the quality of concrete ensured?
Ans. Concrete undergoes rigorous testing, including compression and slump tests, to ensure it meets industry standards.
Q5.What does the future of concrete hold?
Ans. The future includes more eco-friendly production methods, advanced technologies like 3D-printed concrete, and a focus on reducing carbon emissions.